A thorough risk assessment is the first step toward creating effective safety policies and procedures that will move the needle in your organization and identify potential hazards in the workplace.
In this guide, we’ll cover the following points and in the coming weeks, POWERS will continue to post additional deep dives into each of the below topics. You can find all POWERS Research and Industry insights here.
- Why every business needs a Workplace Safety Program
- How to Build a Safety Culture (or Make Yours Even Better)
- How to Identify Hazards with a Risk Assessment Framework
- Safety Program Development: How to Create and Implement Policies
- Incident Investigation: How to Stop Future Safety Incidents
- Safety KPIs to Track for Continuous Improvement
- Top Safety Policies and Procedures for Any Business
———–
A thorough risk assessment is the first step toward creating effective safety policies and procedures that will move the needle in your organization.
The most obvious workplace hazards and claims aren’t always the risks that make the most impact. Since creating and enforcing safety policies takes effort and resources, you want to make sure you’re focusing on the right areas.
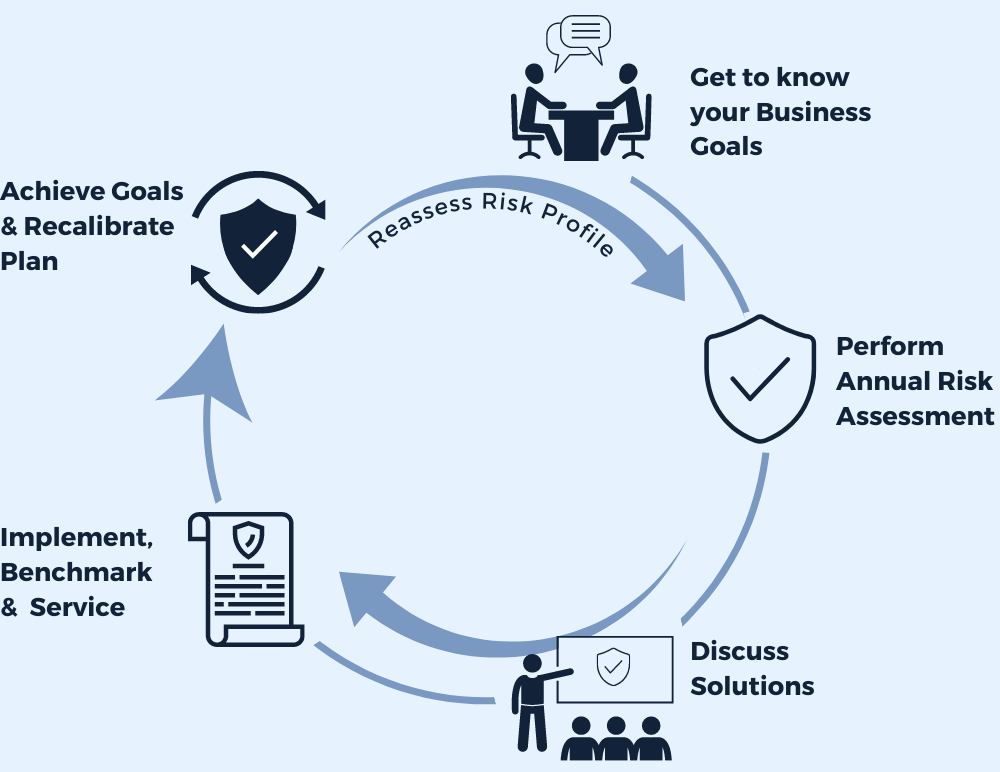
4 steps for a comprehensive safety assessment
At POWERS Insurance, we take every client through a consultative process to identify financially devastating events that could derail their profitability and growth goals. Then, we build and deploy a plan tailored to their industry and business goals.
These are the four foundational steps we use to protect our clients and their stakeholders.
- Identify and assess risks
- Implement risk strategies
- Plan your response to risk events
- Monitor risks
Let’s take a quick look at how to apply each of these 4 steps.
1. Identify and assess potential hazards
The best way to understand where the risk lies in your business is to build a cross-functional team representing a variety of points of view and tenures. Review your company’s past claims, incident reports, near misses, and anecdotal perspectives from team members.
Types of hazards to look for
The safety hazards present in your workplace will depend on your industry. Here are some common categories of hazards and examples.
Physical hazards
- Slip and trip: Uneven floors, cluttered walkways, wet surfaces
- Falls: Unprotected edges, unsafe ladder use
- Impact hazards: Moving machinery, falling objects
- Noise and vibration
- Extreme hot or cold environments
Chemical hazards
- Toxic liquids, gases, fumes, and dust
- Flammable or explosive materials
- Corrosive substances like acids
- Allergens, irritants and otherwise hazardous material
Biomechanical and ergonomic hazards
- Repetitive motions and awkward postures
- Lifting and manual handling of heavy objects
- Inadequate workstation setups
Mechanical hazards
- Entanglement risk: Loose clothing, hair, jewelry
- Crushing and entrapment
- Shearing and cutting
- Lack of machine guards
Environmental hazards
- Severe weather events and earthquakes
- Air quality issues
Psychosocial hazards
- High-stress levels
- Poor work-life balance
- Traumatic incidents
- Bullying and harassment
Electrical hazards
- Shock risks
- Arc flashes and explosions
- Contact with live electrical parts
Biological hazards
- Pathogens like bacteria and viruses
- Vector-borne diseases
Prioritizing hazards
If you come up with a long list, don’t panic. That means you’ve been thorough in your hazard identification. Your goals are to prioritize and devote resources to controlling the most important safety risks.
How can you gauge a hazard’s potential for harm? There are two factors that determine a hazard’s importance: probability and severity. Look at the list of risks you identified and answer two questions for each of them:
- Probability: What is the likelihood that this risk will happen?
- Severity: What are the potential costs (physical, operational, financial) if it does?
2. Reduce exposure to hazards with risk strategies
Once you’ve prioritized your top risks, decide how your company will approach each one. There are four types of risk mitigation:
- Avoid the risk altogether. Sometimes, the best decision is to avoid risk with high probability and severity. Risk avoidance might seem like a no-brainer, but it’s often unrealistic for most risks.
- Transfer the risk to another party. Any work that involves contracts is an opportunity for risk transfer. For example, you can require a subrogation waiver on a subcontractor’s insurance policy. Insurance itself is also a form of risk transference.
- Mitigate and minimize the risk as best you can. This is likely the approach your company will take with most risks. Risk mitigation inherently involves trade-offs. Your job is to compare the cost of control measures to the probability and severity of the risk.
- Accept the risk and its implications. No business is risk-free. Some risks are simply a cost of doing business. For risks that are low probability and low severity, risk acceptance is a reasonable approach. The resources to mitigate, transfer, or avoid the risk are just not worth it.
Mitigating risk
For most of the exposures you identify, you’ll take options 2 and 3. Here are some steps you can take to proactively mitigate the risk your business faces:
- Train employees on your company’s safety, security, and risk response policies.
- Make sure employees have convenient access to personal protective equipment, and know how to use it and when it’s required
- Post compliance standards and safety policies where everyone can see them.
- Create contingency plans so you’re prepared to respond to an incident.
- Get the right insurance policies to transfer the financial burden to your carrier.
A solid risk management plan can prevent incidents from happening in your workplace. It also helps foster goodwill with your insurance carrier by showing that you have a proactive approach to controlling risk.
3. Plan your response to risk events
One of the most important parts of the risk management process is being prepared to act if a risk event does occur. Some risks are unavoidable. For example, no one can prevent natural disasters – the best we can do is be prepared.
Your risk response plan could be as simple as “file an insurance claim.” But the higher priority the risk, the more detailed your response plan should be. If an event has the potential to disrupt business operations in a huge way, you need thorough business continuity and disaster recovery plans.
It’s crucial to document these plans ahead of time and use them to train the relevant employees. Because when minutes matter, you won’t have time to deliberate a response.
4. Monitor risks
The risks you face tomorrow might not be the same as those you face today. Doing a hazard assessment once and letting the report collect dust will not help you protect your business in any tangible way.
It’s vital to monitor your company’s risk profile as it evolves and make sure your responses are still appropriate. Repeat the steps of this risk management plan regularly and keep a pulse on external risk factors.
If you don’t have a dedicated risk manager (or even if you do), this can be a tall order. But without an intentional and consistent process, you could face the unexpected consequences of a risk event. Working with a risk control partner can help you identify and respond to new risks.
Safety assessment FAQs
What are some common hazards to look for during my assessment?
The most common hazards vary by industry, but there are some general hazards to look out for:
- Slip and trip hazards such as cords or tools obstructing walkways
- Fire risks like flammable materials and combustible dust
- Machinery exposures such as rotating and reciprocating motions
- Ergonomic issues like heavy lifting and repetitive motion
How do I assess the level of risk associated with an identified hazard?
There are two factors that determine a risk’s importance: probability and severity. Look at the list of risks you identified and answer two questions for each of them:
- Probability: What is the likelihood that this risk will happen?
- Severity: What are the potential costs if it does?
You can categorize each hazard as low, medium, or high based on your answers to these questions.
How often should I conduct a risk assessment for my business?
At POWERS Insurance, we recommend conducting an assessment annually to keep safety measures current and improvements manageable. Waiting several years between assessments can leave you with long-term exposures and an overwhelming number of improvements needed. You should plan to go through the risk assessment process when a significant change occurs in your business, like big changes in processes, equipment, or leadership.
A successful safety program takes a village
Preventing workplace injuries is an investment worth making. However, those resources can quickly add up. Explore options for outsourcing exposure analysis where you can. Does your workers’ comp carrier provide resources? How about your insurance agent?
All POWERS clients have access to our risk experts as a value-add. We know how to ask the right questions in a full exposure analysis to identify risks that could cause a financial disruption for your business. It’s all about helping you protect your people and reduce insurance costs without huge in-house expenses.
Find out how our experts can help you protect your employees, reduce costs, and boost your return on safety by scheduling a free consultation today.