This post is part of our series, The Ultimate Workplace Safety Guide. Check out our related posts:
- Why Workplace Safety is Important: Every Business Needs a Program
- How to Build a Safety Culture (or Make Yours Even Better)
- How to Identify Hazards with a Risk Assessment Framework
- Safety Program Development: How to Create and Implement Policies
- Incident Investigation: How to Stop Future Safety Incidents
- Safety KPIs to Track for Continuous Improvement
- Top Safety Policies and Procedures for Any Business
Mathematician Karl Pearson said, “That which is measured improves.” If your goal is to improve your safety program, you must track key performance indicators (KPIs) to measure its efficacy.
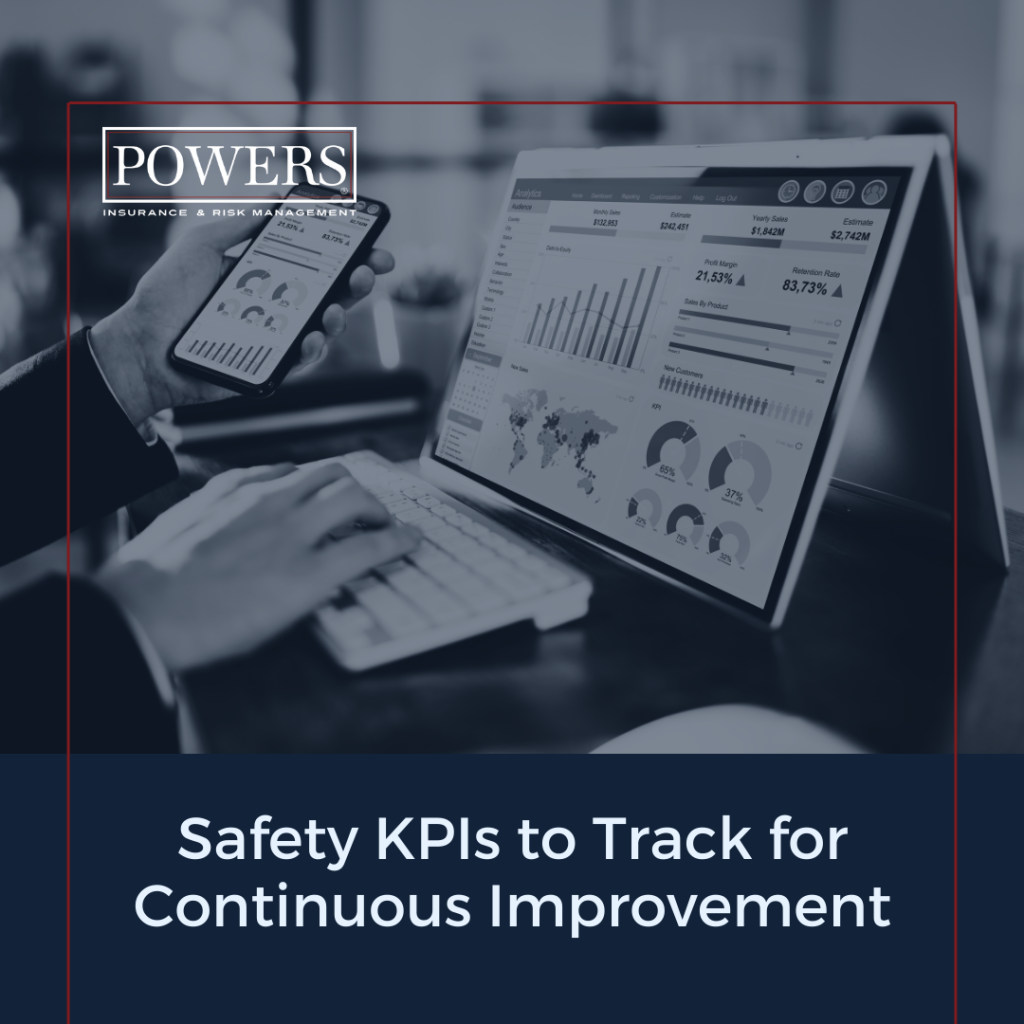
Establishing KPIs: What should be measured?
The metrics most companies track to measure safety performance fall into two categories: lagging and leading indicators.
Lagging indicators
A lagging indicator is a metric that changes after the variable it measures changes. For example, if your company tracks a safety incident rate, you’ll see the rate increase after the number of incidents increases.
Lagging safety indicators are crucial to measure. The problem is that by the time you see concerns reflected in your safety KPIs, accidents are already happening. Employees are already getting hurt.
Common lagging indicators for workplace safety include:
- Recordable incident rate. This metric is a common way to measure trends in the number of incidents your organization has. Learn how to calculate recordable incident rates.
- Lost-time injury frequency rate. This metric measures how frequently you experienced lost-time accidents. Learn how to calculate injury frequency rate.
- Lost-time injury severity rate. This metric measures how severe the accidents you experienced were. Learn how to calculate injury severity rate.
- Near miss rate. Some safety pros consider near misses a leading indicator. However, many agree that by the time a near-miss incident is reported, a significant risk is already present – making it more of a lagging indicator. You can measure this metric in the same way you measure workplace incidents.
Leading indicators
Lagging indicators function as a final “cry for help.” In a perfect world, safety pros would also track metrics that help identify safety concerns before they turn into injuries. These safety metrics are called leading indicators.
For example, if your training completion rate drops from 90% to 75% after a policy change, it’s a sign that your risk of workplace injuries could increase. Seeing a change in this leading indicator is a flag to check whether corrective action is needed.
Common leading indicators include:
- Safety training completion rates. This metric measures awareness and understanding of safety protocols.
- Safety meeting participation. Safety meetings may differ from formal training and could include stand-ups and toolbox talks.
- Safety audit scores. Declining safety audit scores are a serious red flag for employee safety.
- Equipment maintenance records. Well-maintained equipment leads to fewer workplace accidents and injuries. Tracking this metric can help lower the risk of machine-related injuries.
- Operational bottlenecks. Disruptions in workflow or efficiency are common justifications for unsafe behaviors. OSHA gives an example of a hospital where nurses suffered injuries from manually lifting patients. Investigation revealed that lifting equipment was not arriving soon enough when ordered, so nurses were lifting patients themselves to keep work moving. These types of issues depend on your specific organization and may take some digging to uncover.
How to monitor and track safety
After choosing which KPIs are the most beneficial for your safety program, it’s time to decide how to track them. Standardization is the best way to consistently measure your chosen KPIs without feeling overwhelmed or overcommitted.
Standardize safety audits with checklists
Decide when and how to audit your safety KPIs. Updating metrics more frequently will help catch concerns quickly. For smaller, less dynamic companies, annual audits balance prevention with practicality. However, if you have dedicated safety resources, biannual or quarterly audits are even better.
Create standardized checklists and forms to use in the audit. Look for templates from trustworthy sources online, and tailor them to your organization’s needs.
Identify areas for improvement
Have a plan for corrective action if your audit reveals a worsening KPI or one that falls below benchmark. Which team members will be accountable for developing an action plan and executing it? When will you follow up to see whether the KPI has improved?
Consider safety management software
For many smaller organizations, spreadsheets, and email reports work fine for safety reporting. But the manual work involved in auditing, tracking, reporting, and implementing action plans can add up as your company grows.
If you find yourself in this position, it’s time to consider a safety management solution. this type of software can be connected to other business tools for real-time reporting.
Analyzing incident and near-miss data
Having a process for investigating incidents is key to identifying root causes and applying preventive measures. If the reporting system reveals an uptick in incidents, it’s time to explore why.
Ideally, you’ve done a formal incident investigation for every lost-time claim in your organization. If your KPIs reveal trouble in a particular area, review the relevant investigation reports and identify patterns.
The further you dig into the underlying causes of the troubling metric, the more targeted and effective your interventions can be.
Employee feedback and engagement
Tracking KPIs is a fantastic way to quantify your program’s success and identify safety measures for improvement. However, the best systems for continuous improvement include both quantitative and qualitative inputs.
Don’t forget to involve your employees every step of the way. After all, to find out whether something is working, asking the folks who use it will get a much quicker answer than crunching the numbers.
Devote significant effort to developing and maintaining a strong safety culture. This opens feedback channels to help you gauge employee perceptions of safety, training effectiveness, and management’s commitment to health and safety.
Continuous improvement FAQs
Why should a business measure both lagging and leading indicators?
Measuring both lagging and leading indicators can give you a holistic view of your safety program’s performance. Leading indicators help you identify potential safety issues before they escalate into injuries. On the other hand, lagging indicators serve as red flags that serious risks are already present.
How often should a business conduct safety audits and update KPIs?
For smaller, less dynamic organizations, annual safety audits may be sufficient. Larger, rapidly changing organizations face higher risk and can benefit from more frequent updates. For these companies, POWERS recommends quarterly safety audits to identify and address concerns quickly.
A successful safety program takes a village
Preventing injuries is an investment worth making. However, those resources can quickly add up. Explore your options for outsourcing safety support where you can. Does your workers’ comp carrier provide resources? How about your agent?
All POWERS clients have access to safety education and loss control analysis experts as a value-add. It’s all about helping you protect your people and reduce insurance costs without huge in-house expenses.
Find out how our experts can help you protect your employees, reduce costs, and boost your return on safety by scheduling a free consultation today.
Up next: Top Safety Policies and Procedures for Any Business |